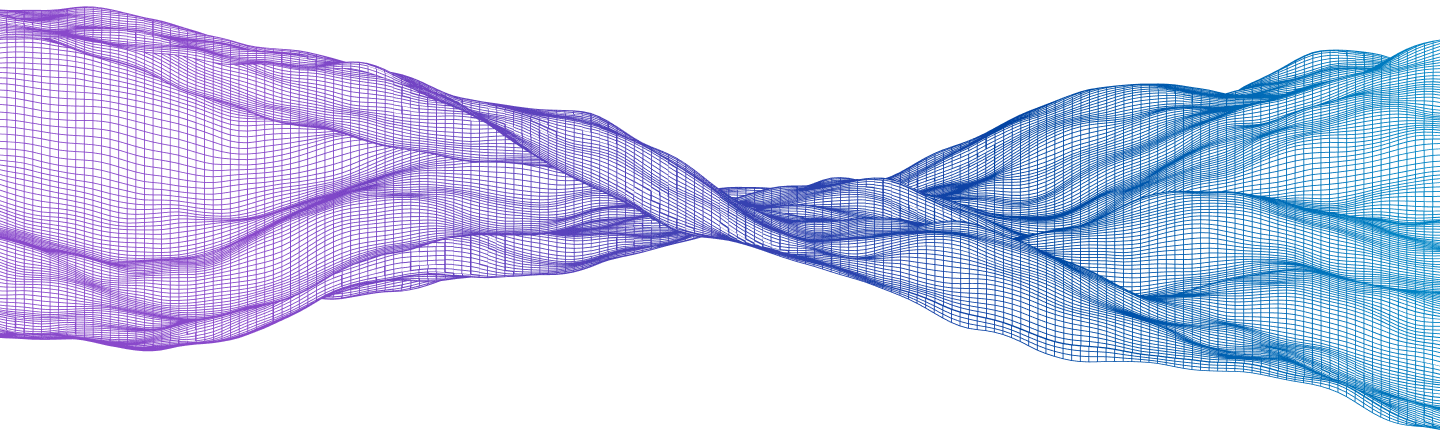
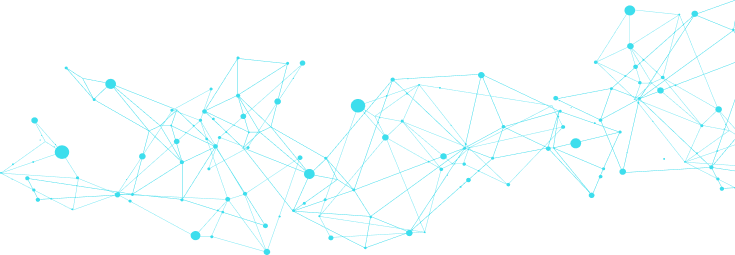
Roadmap for IDD
Bring Integrated Digital Delivery into your practices with these detailed use cases and practical implementation strategies
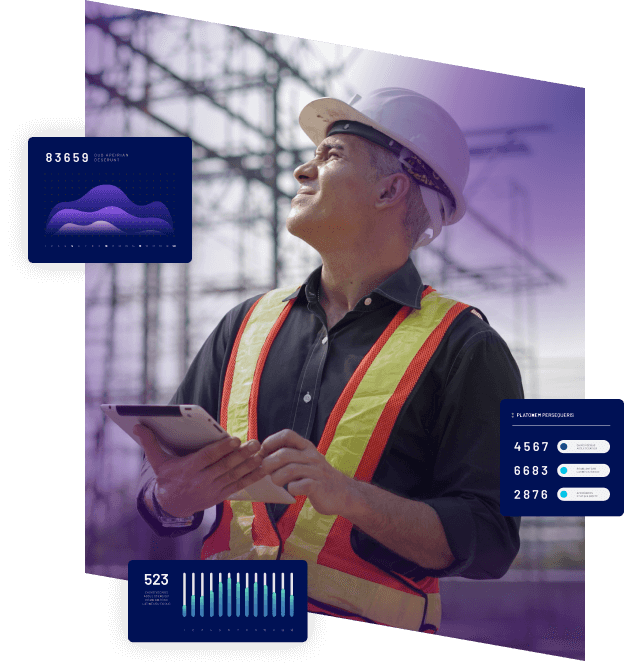
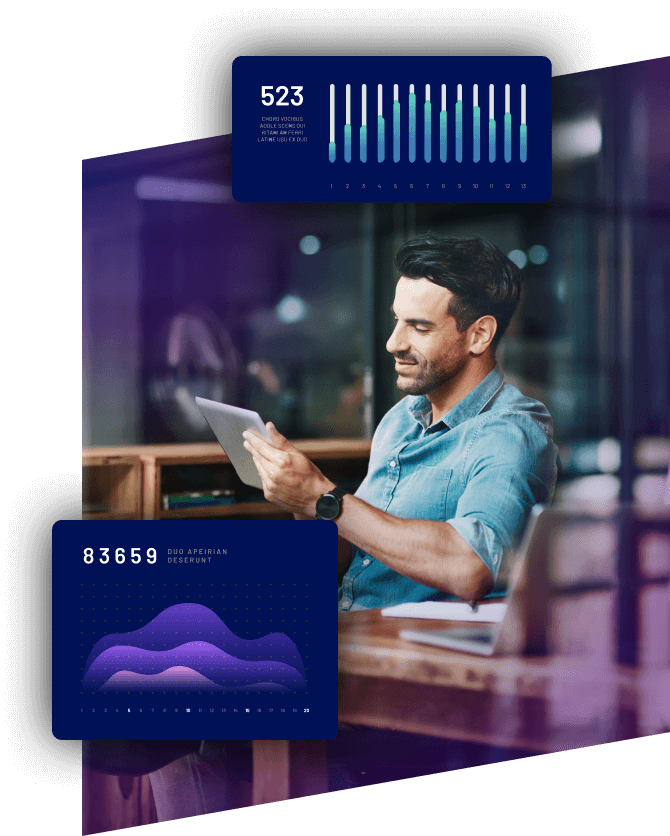
Getting Started With Integrated Digital Delivery
Integrated Digital Delivery (IDD) leverages digital technologies to transform project delivery and asset management across the AECO sector. By implementing IDD, organizations can streamline workflows, improve collaboration, and achieve higher efficiency throughout the project lifecycle.
Roadmap to a Successful IDD Implementation
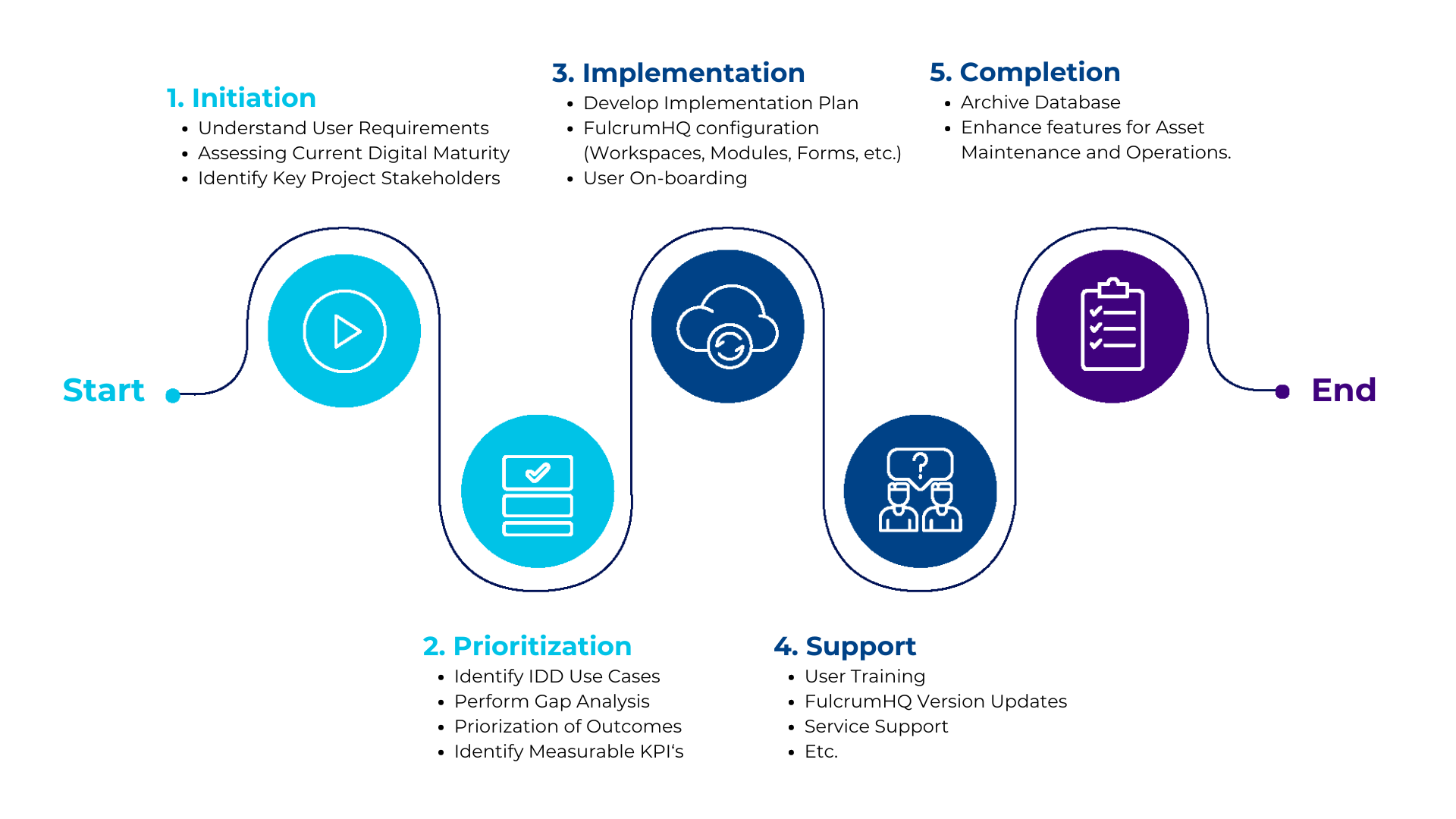
IDD Use Cases Across the Project Lifecycle
Unify your project ecosystem projects with a single end-to-end construction management platform with BIM and advanced model checking at its core. Explore our full platform capabilities.
Initiation
• Understand User Requirements
• Assessing Current Digital Maturity Initiation
• Identify Key Project Stakeholders
Prioritization
• Identify IDD Use Cases
• Perform Gap Analysis
• Prioritization of Outcomes
• Identify Measurable KPI’s
Implementation
• Develop Implementation Plan
• FulcrumHQ configuration (Workspaces, Modules, Forms etc.)
• User On-boarding
Support
• User Training
• FulcrumHQ Version Updates
• Service Support
• Etc.
Completion
• Archive Database
• Enhance features for Asset Maintenance and Operations.
FulcrumHQ Capabilities
Transform the way your teams design, develop and operate the built environment of tomorrow. We empower owners, contractors and designers to unlock unparalleled efficiency and collaboration in every phase of the asset lifecycle.
Collaboration & Communication
Discover modern digital workspaces with highly configurable, integrated and streamlined information management for secure and smart collaboration.
AI powered quality control and model checking
State-of-the-art BIM for greenfield and brownfield projects with machine-powered algorithms to support EIR, AIR, and regulatory compliance, and digital twinning.
Field management and checklists
Comprehensive site management with smart forms and checklists for quality, safety, permits to work and other site functions. Available as native apps on iOS and Android.
Interoperability APIs and Open Standards
Manage digital requests for information (RFIs) and digital QA/QC checks with onsite access to current project information and models. Supports safety, defect management, and automated asset registration.
Computational BIM with GIS Integration
Cohesive GIS and BIM platform set ups for more efficient and smarter operations brought together from diverse range of systems, devices, and sensors.
Analytics and Dashboards
Rich analytics and insight for informed decision making for construction projects and infrastructure operations through ingestion of data from the platform’s native APIs and external data sources.
Security and Data Access
Access intelligent construction management using a common data environment (CDE), powered by advanced AI.
IDD Use Case 1
Digital Request for Information (RFI)
Use digital technology to request information or facilitate communication regarding any issues stemming from building works.
Standard Process
-
Paper-Based RFIs: RFIs that are managed via paper forms require extensive printing and physical handling.
-
Manual Transmission: RFIs may be sent out manually for validation and approvals, a time-consuming and error-prone process.
-
Risk of Loss and Delay: RFIs could be misplaced, accidentally destroyed, or delayed if approvers are unavailable.
-
Record Keeping: If RFIs are manually stored, substantial physical space and effort for archival and retrieval is required.
Enhanced Process Using FulcrumHQ
- Digital Forms: Transition to customized, digital forms that are centrally stored within FulcrumHQ’s Common Data Environment (CDE), enhancing the efficiency and traceability of the RFI process.
- Automated Workflows: Integrate automated workflows to facilitate quick and accurate validations and approvals, significantly speeding up the RFI process.
- Secure and Accessible Records: Digital records of RFIs are securely stored and readily accessible within the system, easing the process of audits and historical data retrieval.
- Mobile Accessibility: Enable site staff to fill out and manage RFIs efficiently on-site using the FulcrumHQ mobile app, ensuring real-time updates and immediate submission.
Key Benefits
- Streamlined Workflow: The digitalization of paper-based RFIs revolutionizes the entire workflow. By transitioning from printing to digital forms, filling them out, transmitting them through each approval stage, and retrieving them when needed, every step becomes more efficient and integrated.
- Increased Productivity: Through the standardization of forms, the implementation of automated workflows, coordinated information sharing, and the use of handheld devices to access a centralized information source, productivity related to RFIs can increase significantly. Estimates suggest improvements in the range of 25% to 37%, greatly enhancing overall project efficiency.
-
Step 1: Review historical data to estimate the average man-hours required to complete an RFI. (i.e. Difference between start and end dates)
-
Step 2: Measure the time taken to complete RFI using FulcrumHQ. (Note: For increased accuracy, measure the average time taken over a series of RFIs.)
-
Step 3: Calculate the difference in man-hours between steps 1 and 2.
Address Pace and Rhythm Shifts: Anticipate employee concerns about adapting to a new work pace or rhythm. Implement phased changes, provide training, and offer support resources to ease the transition.
Way of Measurement
Step 1
Review historical data to estimate the average man-hours required to complete an RFI. (i.e. Difference between start and end dates)
Step 2
Measure the time taken to complete RFI using FulcrumHQ. (Note, for increased accuracy, measure the average time taken over a series of RFIs)
Step 3
Calculate the difference in man-hours between steps 1 and 2
IDD Use Case 2
Integrated Concurrent Engineering (ICE) Meetings
Conduct an Integrated Concurrent Engineering (ICE) meeting using digital technology and Building Information Modeling (BIM).
Standard Process
-
Silos and Uncoordinated Efforts: Various stakeholders required for the delivery of a project are working in silos resulting in uncoordinated decision making.
-
Delayed Decision-Making: Decision-making is challenging and can sometimes take weeks.
Enhanced Process Using FulcrumHQ
- Collaboration: ICE meetings will be held throughout the construction process with key stakeholders being engaged in decision making process using FulcrumHQ as the Common Data Environment (CDE) and leverage the collaboration features to provide modern digital workspaces with high configurability.
- Integration: These will also have integrated document and content management to support advance 3D BIM workflows such as quantity takeoffs, clash detection and visualization.
Key Benefits
- Time: The use of this system reduces the time taken for resolving coordination problems and rework while project members enjoy a more efficient design and decision-making process.*
- Quality: Improvements by using innovative digital solutions and to reduce potential design changes downstream in the construction process.
- Reduce Revisions: Improvements by using innovative digital solutions and to reduce potential design changes downstream in the construction process.
* A case study by Stanford University’s Center for Integrated Facility Engineering found that ICE sessions helped resolve 80 percent of issues within teams in 30 minutes or less. Moreover, 80 percent of all other issues were resolved in four hours or less when stakeholders were co-located in the Big Room.
-
Step 1: Analyze historical data to estimate the average man-hours spent on design coordination meetings and the number of design changes and iterations throughout a project.
-
Step 2: Record the time taken to complete ICE meetings using FulcrumHQ and note the number of design changes and iterations throughout the project.
-
Step 3: Determine the difference in man-hours between steps 1 and 2.
- Unify Stakeholders: Bridge differences by fostering open communication and establishing transparent processes, considering diverse workstyles and cultures.
- Empower Decisions: Ensure key decision-makers are readily available or represented by designated substitutes to expedite timely and informed choices.
IDD Use Case 3
Visualization and Design Checks
Utilize a BIM model, a digital 3-dimensional model, or immersive technology to visualize the building’s design, seek feedback, and validate it.
Standard Process
-
2D Design Reviews: Design consultants and builders conduct design reviews using 2D drawings.
-
Error Prone: This approach often encounters challenges in ensuring compliance with all statutory rules across multiple agencies. The process is prone to errors and can be incomplete due to the large number of elements that need checking.
Enhanced Process Using FulcrumHQ
- 3D Design Reviews: All stakeholders, key decision-makers, and designers can view federated IFC models using FulcrumHQ’s 3D BIM Viewer, which integrates with immersive technologies like AR/VR.
- AI Clash Detection: Leveraging FulcrumHQ’s BIM capabilities, users can augment machine intelligence into their traditional compliance workflows, enabling automated clash detection and management of every element in the IFC.
Key Benefits
- Time: There is a significant reduction in the time required to resolve compliance issues and rework, allowing project members to enjoy a more efficient design and decision-making process.
- Quality: Innovative digital solutions enhance quality by identifying clashes and non-compliances during the design stage, rather than during construction.
- Increase Contract Value: Utilizing clash detection in BIM can save an estimated 20% of contract value. According to a survey by Dodge Construction & Analytics, 46% of respondents reported significant value from improved multi-party communication and understanding due to 3D visualization. Additionally, 53% of respondents agreed that BIM supports access to analysis and coordination tools, enabling informed design and construction decisions.
- 3D Design Reviews: FulcrumHQ’s web-based platform enables users to view and federate large, high-fidelity 3D BIM models directly from the browser. FulcrumHQ can also integrate with third-party VR software to view rendered models stored in FulcrumHQ’s CDE.
-
Step 1: Review historical data to estimate the average hours spent on design and compliance checks throughout a project and the number of clashes on-site requiring immediate rectification.
-
Step 2: Measure the time taken to complete design checks meetings using FulcrumHQ and the number of design clashes identified during construction.
-
Step 3: Calculate the difference in hours between steps 1 & 2.
Even with machine intelligence’s (MI) crucial insights, it’s valuable to remember that Licensed Design Professionals or Qualified Persons must exercise sound judgment and critical thinking when utilizing MI outputs, ensuring they align with professional standards and established engineering practices.
IDD Use Case 4
Digital Submittals and Approvals
Use digital technology to submit and obtain approval relating to the design of the building or any component involved in the building works.
Standard Process
-
Manual Processes: Obtaining design approvals requires a manual process, and transmittals are typically done only via email among the recipients in the email thread.
-
Limited Paper Trail: The audit trail for submissions and approvals is limited.
-
Potential for Missed Approvals: If not managed effectively, building works could potentially be carried out without the necessary design approvals.
Enhanced Process Using FulcrumHQ
- Centralized Processes: All submissions and correspondences for approvals will be done on FulcrumHQ.
- Reliable Revisions: By leveraging FulcrumHQ’s collaboration features, users will be able to digitally submit designs, and trigger automated workflows for approvals. Approvers are notified when a new submission is made. This streamlines the checking and approval process thus resulting in more reliable outcomes which enable traceability and auditability for future reference to all involved in the project
Key Benefits
- Time: Project teams can potentially enjoy a 46-67% reduction in time spent obtaining design approvals, according to a Dodge Construction Report. This is due to improved work tracking and documentation of design submissions and approvals, which leads to less potential rework on site and increased productivity.
- Safety: Only approved submissions will be physically constructed on-site, which mitigates the safety risks of unapproved construction
- Seamless Reviews: FulcrumHQ’s web-based platform enables users to digitally submit designs and trigger automated workflows for approvals. Approvers are notified when a new submission is made. Users can also create, and track issues found during the design process and export/import issues in BCF format.
- Streamlined Processes: Project teams can potentially enjoy a 46-67% reduction in time spent obtaining design approvals, according to a Dodge Construction Report.
-
Step 1: Review historical data to estimate the average hours spent on locating and retrieving historical project data.
-
Step 2: Measure the time taken to locate and retrieve historical project data using FulcrumHQ.
-
Step 3: Calculate the difference in hours between steps 1 and 2.
Configuring submission workflows to align with your organization’s specific needs could be a time-consuming process at the start of implementation.
But this is a one-time setup that will ease the challenges of working in siloed and disparate environments.
IDD Use Case 5
BIM-based Documentation
Prepare documents based on information primarily generated from a BIM model.
Standard Process
-
Non-Integrated Tools: Design consultants and builders employ various non-integrated tools and workflows to generate project documents.
-
Siloed Work: Instead of collaborating to establish a single source of truth, stakeholders continue to work in silos.
-
Errors and Delays: This approach often leads to the creation of duplicate information, potentially causing errors and delays downstream.
Enhanced Process Using FulcrumHQ
- Unified Collaboration: The project teams will use FulcrumHQ to collaborate on their designs using the 3D Viewer and correspondence features. Once designs are fully coordinated, designers can use a combination of their respective BIM Model Authoring tools (e.g. Revit, Tekla etc.) and FulcrumHQ to generate all project documents including 2D Drawings, Schedules, tender specifications etc. All stakeholders will have easy access to the latest project documents via FulcrumHQ throughout the project lifecycle.
Key Benefits
- Time: Project teams can expect a reduction in time spent retrieving the latest project information. This is because all project data is linked to the BIM model and is easily accessible via FulcrumHQ.
- Safety: All project documentation will originate from a single-source-of-truth and therefore will be uniform throughout all documents. This will reduced discrepancies and improve productivity.
- 3D Tools: FulcrumHQ’s web-based platform enables users to work collaboratively on their designs using the 3D Viewer and correspondence tools. Once designs are fully coordinated, designers can use a combination of their respective BIM Model Authoring tools (e.g. Revit, Tekla etc.) and FulcrumHQ to generate all project documents including 2D Drawings, Schedules, tender specifications etc.
- Single Source of Truth: All project documentation will originate from a single-source-of-truth and therefore will be uniform throughout all documents.
-
Step 1: Review historical data to estimate the average man-hours spent on locating and retrieving historical project data.
-
Step 2: Measure the time taken to locate and retrieve historical project data using FulcrumHQ.
-
Step 3: Calculate the difference in man-hours between steps 1 and 2.
Ensure alignment with all stakeholders involved in the BIM process to diligently upload relevant documentation.
The naming convention or taxonomy of the uploaded documents should be accurate.
IDD Use Case 6
BIM-based Cost Estimation
Estimate costs at various stages of the building works based on information generated from a BIM model.
Standard Process
-
Manual Processes: The Quantity Take Off (QTO) process is done manually and tabulated in a spreadsheet by visually inspecting designs from each discipline.
-
Error Prone: This process time is consuming and error prone, which potentially results in incorrect cost estimations for the project causing significant cost overruns or delays in the project downstream.
Enhanced Process Using FulcrumHQ
- Increased Efficiency: By leveraging FulcrumHQ’s 3D BIM viewer, users are able to efficiently search and query BIM data within the IFC files to automatically extract QTO information.
- Accurate Estimations: Information on the specific unit rates for each element can also be imported to FulcrumHQ to enable users to estimate the total costs.
- Repeatable Processes: This process can be repeated at any stage of the project and to support progress claims.
Key Benefits
- Time: Expect significant time savings on manual QTO tasks and progress claim quantification thanks to streamlined workflows within the system.
- Quality: The 3D models provide component count and nested data such as area, volume and material quantities thus reducing the error in the traditional QTO process.
- Cost Forecasts: Any potential implications to project budgets due to design changes are easily computable throughout the project lifecycle.
- Web-based application: Using FulcrumHQ’s Query feature, users will have the ability to easily interrogate the 3D Model directly from the browserbased BIM viewer to extract highly accurate Quantity Take-Offs (QTO) information. The QTO will be the base to provide high-fidelity costing information on the project.
-
Step 1: Review historical data to estimate the average man-hours spent on manual QTO process and applying unit rates to determine the Bill of Material (BOM).
-
Step 2: Measure the time taken extract QTO and BOM information FulcrumHQ and the time taken to quantify progress claim amounts.
-
Step 3: Calculate the difference in man-hours between steps 1 & 2.
Prepare a Detailed 3D Model: Ensure your 3D model is accurate and complete for precise Quantity Take-Off (QTO). This will optimize material and cost estimations.
Maintain Updated Unit Rates: Regularly review and adjust unit rates for materials and labor to reflect current market fluctuations. Accurate rates ensure reliable cost estimations.
IDD Use Case 7
Digital Logistics
Use digital technology to plan the prefabrication production schedule of the building works, and digitally track and monitor the production, delivery and installation of prefabricated components.
Standard Process
-
Manual Processes: The processes of monitoring production, delivery, and installation of prefabricated components are manually tracked using paper-based forms. These forms are only displayed on charts located in the site office.
-
Risk of Documents Misplaced or Destroyed: There exists a risk of tracking documents being misplaced or destroyed accidentally. This could potentially lead to site delays or waste due to over-production.
Enhanced Process Using FulcrumHQ
- Mobile, Unified Processes: The status of the fabrication, delivery, receipt and installation of prefabricated components will be updated and shared via FulcrumHQ Field module.
- Easily Viewable Information: Users granted with access will be able to view the shared information for easy monitoring and tracking of prefabricated components directly from the BIM models.
- On-Site Reviews: Based on the planning schedules, users can easily identify prefabricated elements to be requested for delivery to site when required.
Key Benefits
- Time: Reduce wasted time and effort through better recording, drawing coordination, onsite checking, and logistics tracking, leading to a significant productivity increase
- Planning: This process also reduces the risk of delays for procuring prefabricated elements and promotes better scheduling and planning.
- Waste Reduction: The process mitigates the risks of over-production and storage of prefabricated elements on site. If elements are not stored adequately on-site, there is a risk of damage and therefore waste.
- Improved Measurement: Measure key metrics across the entire logistic workflow undertaken on FulcrumHQ.
- 3D Models: FulcrumHQ’s web-based platform displaying 3D BIM models to track status of fabrication, delivery, receipt and installation of prefabricated components
- Mobile Application: Allows for on-site verification and real-time progress updates via QR code.
-
Step 1: Map out current process and steps from start to finish of the logistics workflow. Identify the key metrics including time taken at each step, no. of people/workers involved and average idle time between steps.
-
Step 2: Measure key metrics across the entire logistic workflow undertaken on FulcrumHQ.
-
Step 3: Tabulate the differences in key metrics (e.g., man-hours, number of workers, etc.) between steps 1 and 2.
Prepare a Detailed 3D Model: Ensure your 3D model is accurate and complete for precise Quantity Take-Off (QTO). This will optimize material and cost estimations.
Maintain Updated Unit Rates: Regularly review and adjust unit rates for materials and labor to reflect current market fluctuations. Accurate rates ensure reliable cost estimations.
IDD Use Case 8
Digital Construction Scheduling and Sequencing
Use digital scheduling to plan and monitor the construction activities of the building works.
Standard Process
-
Manual Processes: Construction planning, scheduling and sequencing is done manually and without integration with 3D BIM information. The information is displayed on Gantt chart located within the site office.
-
Lack of Visibility: Accessing this Gantt chart can be challenging for many project stakeholders. This difficulty can potentially cause on-site delays due to lack of coordination and communication.
Enhanced Process Using FulcrumHQ
- One Source of Truth: FulcrumHQ CDE be a singlesource- of-truth for all construction scheduling and sequencing information. Leveraging on the DesignSync module, users can upload 4D BIM information from the native desktop applications directly into the CDE.
- Easily Accessible Information: Videos from 4D BIM sequencing tools can be uploaded and reviewed directly from FulcrumHQ’s web application making the information easily accessible to all stakeholders involved in the project.
Key Benefits
- Time: Experience significant productivity gains thanks to improved recording, drawing coordination, on-site checking, and logistics tracking.
- Planning: This process also reduces the risk of delays for procuring prefabricated elements and promotes better scheduling and planning.
- Waste Reduction: The process mitigates the risks of over-production and storage of prefabricated elements on site. If elements are not stored adequately on-site, there is a risk of damage and therefore waste.
- 3D Viewer: FulcrumHQ’s web-based information exchange platform enables users to visualize construction schedules directly from 3D viewer based on the relevant metadata inputs present in the model (e.g. Planned start date, actual start date, planned end date etc.)
-
Step 1: Measure the time taken to access key construction and scheduling information. Map out current process and steps from start to finish of the scheduling workflow. Identify the key metrics including time taken at each step, no. of people/workers involved and average idle time between steps.
-
Step 2: Measure key metrics across the entire scheduling workflow undertaken on FulcrumHQ.
-
Step 3: Tabulate the difference in key metrics (e.g. Man-hours, no. of workers etc.) between steps 1 & 2.
Optimize your 3D Model: Ensure your 3D model is detailed and construction-ready for accurate scheduling and sequencing. Refine the level of detail as needed.
Acquire 4D BIM Expertise: Invest in training or specialist resources to build your team’s skills in 4D BIM modeling software. This ensures efficient construction planning.
IDD Use Case 9
Digital Progress Monitoring
Use digital solutions or digital scanning to track and monitor the progress of the building works.
Standard Process
-
Siloed, Manual Processes: On-site progress is visually assessed solely by Resident Engineers (REs) or Registered Technical Observers (RTOs). This information is manually compared to the overall construction schedule and presented in weekly progress report meetings.
Enhanced Process Using FulcrumHQ
- Easily Viewable Information: Information regarding the planned start and end dates for the construction of each building element is accessible directly from FulcrumHQ. By querying this information, users can monitor the construction activities while dashboard functionality provides an overview of Project ‘health’ and status.
- Streamlined Processes: Eliminate the ‘double handling’ of information, provides common template for update of project status with results immediately translated into graphs and visualizations.
Key Benefits
- Real-Time insights into Construction Progress: All stakeholders involved in the construction project will have access to real-time information of the site.
- Time: Processes that are behind schedule can be easily identified and rectified prior to waiting for weekly progress meetings.
- Productivity: Site and design teams are able to view the overall progress status of the site to ensure that the project is on track. Any potential bottlenecks can be resolved prior to causing delays on site.
- Increased Visibility: Site and design teams are able to view the overall progress status of the site to ensure that the project is on track.
- Customizable Views: FulcrumHQ’s web-based information exchange platform enables users to view construction progress visually directly from the browser. This information will be presented in customisable dashboards that are able to effectively report the overall health of the project at a single glance.
N/A
Dashboards are only reflective of the data that is fed into them, therefore the quantity and quality of the data collected must be good.
The dashboards should be designed to be clear, concise and to support decision making.
IDD Use Case 10
Digital QA/QC Inspections
Use digital solutions to record the observations from site inspections of the building works and track the necessary follow-up actions taken.
Standard Process
-
Manual Processes: All QA/QC reports are recorded manually using paper-based forms. These reports are then stored in folders in the siteoffice and any remedial action for the management of defects will require documents and information pertaining to the defects to be relayed to the responsible party for further action.
-
Manual Communication: Supplementary information, such as images or videos, is directly sent to the respective stakeholders via WhatsApp or email.
Enhanced Process Using FulcrumHQ
- Mobile Accessibility: By leveraging FulcrumHQ Field Application, users can access BIM data and carry out QA/QC works by accessing customised digital inspection checklists directly onsite from a mobile device. Markups done on-site can be uploaded and sent back to drawing board for subsequent updates.
- Easily Accessible Information: All QA/QC reports and supporting information is easily accessible directly from FulcrumHQ for all stakeholders.
Key Benefits
- Streamlined Workflow: The benefits for digitalizing paper-based forms can be realized across the entire workflow, from printing QA/QC checklists, filling in the forms, transmitting reports for each stage of approval and finally achieving or retrieving the Reports when required.
- Time: Teams can expect increase in productivity on time spent on QA/QC checking can be realized through form standardization, automated workflows, coordinated information amongst all users, ease of using handheld device and one stop information centre.
- Increased Accuracy: Implementing objective measurement tools can enhance report accuracy and reduce inconsistencies.
- Increased Visibility: FulcrumHQ’s web-based information exchange platform enables users to view all QA/QC inspections information directly from the browser. The platform allows users to create customisable workflows to track and manage the issues identified during the inspections.
- Mobile Accessibility: The Mobile Application provides a platform for users to capture data regarding the QA/QC inspections directly from the construction site.
-
Step 1: Review the steps taken to complete the current QA/QC inspection workflow from start to finish. Identify the key metrics including time taken at each step, no. of people/workers involved and average idle time between steps.
-
Step 2: Measure key metrics across this entire workflow undertaken on FulcrumHQ.
-
Step 3: Tabulate the difference in key metrics (e.g. Man-hours, no. of workers etc.) between steps 1 and 2.
Sole reliance on visual inspection in QA/QC poses risks of inconsistent defect evaluations due to subjectivity based on inspector experience. Implementing objective measurement tools can enhance report accuracy and reduce inconsistencies.
IDD Use Case 11
Digital Defects Management
Use digital checklists or digital dashboards to manage and track the defects of the building works and the rectification of those defects.
Standard Process
-
Manual Processes: All defects observed on-site are recorded manually using paperbased forms. These forms are then stored in folders in the site-office and any remedial action for the management of defects will require documents and information pertaining to the defects to be relayed to the responsible party for further action.
-
Error Prone: This process is error-prone and can results in various defects not being fixed during the DLP period which may potentially cause more serious problems to the owners at a later stage.
Enhanced Process Using FulcrumHQ
- Increased Visibility: The digital inspection forms used during the QA/QC checks and findings with relevant photos will be uploaded to the FulcrumHQ and all stakeholders will have easy access to the information in real-time.
- Automated Processes: The digital forms can be configured to trigger automated workflows to effectively manage the defects identified during the QA/QC inspections.
- 3D BIM Models: All defects information is easily visualized by linking it directly to the 3D BIM models.
Key Benefits
- Improved Quality: Effective defect management processes can help to reduce the number of defects and related costs by identifying problems in the construction methodology early on in the project by analysing the trends of defects being recorded.
- Time: By improving the quality of work, there can be decrease in the number of defects that need to be remedied on site.
- Increased Quality: By improving the quality of work, there can be decrease in the number of defects that need to be remedied on site.
- Web-Based Information: FulcrumHQ’s web-based information exchange platform enables users to view all defects information directly from the browser. The platform allows users to create customisable workflows to track and manage the issues identified during the inspections.
- Mobile Information: The Mobile Application provides a platform for users to capture data regarding the defects directly from the construction site
-
Step 1: Review the steps taken to complete the current Defects Management workflow from start to finish. Identify the key metrics including time taken at each step, no. of people/workers involved and average idle time between steps.
-
Step 2: Measure key metrics across this entire workflow undertaken on FulcrumHQ.
-
Step 3: Tabulate the difference in key metrics (e.g. Man-hours, no. of workers etc.) between steps 1 & 2.
Define Defect-Specific Workflows: This use case is dependent on the defects that are identified during the QA/QC inspections.
Maintain & Iterate: Establish initial workflows and continuously adjust them to optimize response times and ensure notifications reach the right teams for timely resolutions.
IDD Use Case 12
Digital Handover
Use digital technology to generate and digitally handover.
Standard Process
-
Paper-based Documentation: After TOP, all building information is handed to the owners. This typically consists of large amounts of paper-based documentation for As-built drawings, equipment manufacturer’s specifications and warranties and other O&M manuals etc.
-
Potential for Misplaced Documents: There is a tendency for these documents to be misplaced or damaged throughout the design life of the building and therefore not available when required during the O&M phase of the project.
Enhanced Process Using FulcrumHQ
- Electronic Records: All the defects identified will be recorded and summarized and customised reports can be generated according using FulcrumHQ.
- 3D and VR Scans: Users can inspect the site using 3D scanner or VR goggles through virtual mock-ups.
- Centralized Information: As such, a data-rich Asset Information Model, containing all relevant information of the building from concept to as-built is stored centrally in FulcrumHQ and will be handed over to the client.
Key Benefits
- Time: Better recording, drawing coordination, on-site QA/QC checking, and defects management are estimated to increase in productivity.
- Digital Record: There will be a digital record that will provide an auditable history of all as-built building information (including defects and rectification works) that has been collected to date. This record will also serve as a repository for easily accessing building information in the future where required (e.g. during A&A or maintenance works). Based on a survey by Dodge Construction, owners are particularly supportive of BIM for digital handover, with 90% giving medium or high impact ratings to better construction documents and 88% to improved constructability.
- Centralized Information: FulcrumHQ’s web-based information exchange platform enables users to view all project information from a single-pane-of-glass view. This Includes all building information collected during the course of the construction, the as-built information and the information from defects and rectification works found during the DLP period.
-
Step 1: Measure the estimated average man-hours spent on the end-to-end handover process. This includes the checking and inspecting building elements, the time taken for recording all defects identified and the follow up action to rectify and close out issues.
-
Step 2: Measure the time taken to complete handover workflows from start to finish using FulcrumHQ.
-
Step 3: Calculate the difference in man-hours between steps 1 and 2.
Establish Naming & Tagging Standards: Align with best practices (e.g., COBie) and Owner’s BEP/OIR requirements to define a standard naming and tagging system for asset information. Ensure consistency and searchability throughout the project lifecycle.
Streamline Asset Management: Utilize the established system to support a richer Asset Information Management and Registration Process, optimizing data capture and facilitating future maintenance and operations.
IDD Use Case 13
Real-time Monitoring of Asset Performance
Set up a digital platform to monitor the real-time performance and track the key operating parameters of a physical asset built as part of the building works.
Standard Process
-
Delayed Monitoring: Assets are not monitored in real-time. As a result, operating parameters are only tracked and captured retrospectively.
Enhanced Process Using FulcrumHQ
- Track Real-Time Performance: Tracking of real-time performance and operating parameters of physical assets can be viewed directly from FulcrumHQ’s Insights Module.
- Sophisticated Integrations: This is done via integration with BMS or specialist IoT equipment installed in the building to track asset performance. FulcrumHQ’s Interop Module will facilitate this integration using APIs to send/receive information in real-time, and to leverage on FulcrumHQ as a CDE to store all required data.
Key Benefits
- Cost: Energy consumption savings can be realised by implementing real-time monitoring of assets performance.
- Quality: By analyzing asset performance, maintenance activities can be prioritized to reduce break-downs and lapses in operation.
-
Step 1: Measure baseline energy consumption of building systems (e.g., AHU, Chiller etc.) without monitoring asset performance.
-
Step 2: Measure energy consumption of building after monitoring and making modifications based on findings to optimize asset performance.
-
Step 3: Calculate the difference in man-hours between steps 1 and 2.
It is important to have a clear understanding of the desired outcomes your organization wants to achieve by monitoring assets in real-time. If not, potentially large amounts of data will be collected which can significantly increase the data-storage costs.
IDD Use Case 14
Digital Operations and Maintenance
Set up a digital platform to integrate other technologies to perform the operations or maintenance of a physical asset that is built as part of the building works.
Standard Process
-
Non-Unified Tools: FM teams are currently using various tools combining both digital and non-digital processes to manage the operations and maintenance of physical assets.
-
Outdated Information: Relevant building information for carrying out maintenance works (e.g., As-built drawings, O&M manuals, warrantees etc.) are not easily accessible or up-todate which can result in delays, ineffective facility management and potential disruption to building operations.
Enhanced Process Using FulcrumHQ
- Interoperability: By leveraging FulcrumHQ’s Interop Integration capability, FM teams have access to data-rich BIM models which seamlessly integrates to other CAFM systems via APIs to provide a single-pane-of-glass view to support and manage the all O&M functions. This will promote effective communication, coordination and collaboration with all stakeholders involved thus enabling organizations to shift from reactive/ time-based maintenance regimes to predictive/ prescriptive ones.
Key Benefits
- Time: Teams can reduce the amount of time spent on manual operations of the QTO process and quantifying progress claims.
- Quality: The 3D models provide component count and nested data such as area, volume and material quantities thus reducing the error in the traditional QTO process.
- Cost & Sustainability: Approximately 10% increase in savings in paper print out for handing over and automated checking and trail searching enabled by Fulcrum. process.
- Web-based Information: FulcrumHQ’s web-based information exchange platform displaying asset information (e.g., Model/ Make, Serial numbers, Historical O&M records, Manufacturer details, O&M manuals, Warrantees, etc.)
- Easily Viewable Information: Display building performance information (e.g., Energy consumption, utilization, efficiency, etc.)
- Sophisticated Integrations: Integration with CMMS systems.
-
Step 1: Review historical data to estimate the average man-hours spent on obtaining, printing and communicating relevant building information for maintenance works.
-
Step 2: Measure the time taken extract QTO and BOM information FulcrumHQ and the time taken to quantify progress claim amounts.
-
Step 3: Calculate the difference in man-hours between steps 1 and 2.
Engage Facility Managers Early: Incorporate Facility Managers from the project’s outset: Include them in design and construction phases to familiarize them with BIM and its benefits.
Bridge the Knowledge Gap: Offer training sessions or workshops on BIM fundamentals and its value for facility management. This empowers them to leverage BIM data effectively.
Challenges with Brownfield BIM: Address data acquisition and develop a plan for gathering existing building data through scans, surveys, and historical documentation.
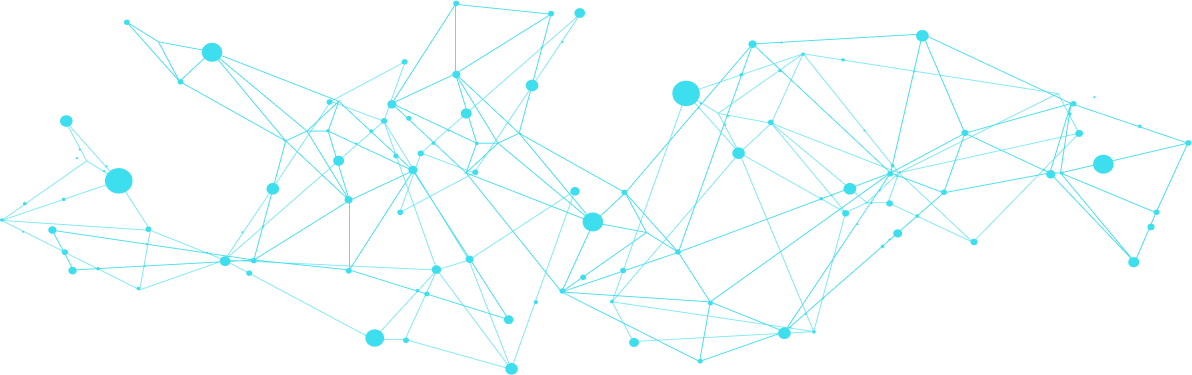
Turn your vision into reality
Leverage the full power of tomorrow's BIM solutions, today. We work with critical stakeholders involved in every aspect of project and portfolio management to create impactful, reliable and sustainable outcomes.
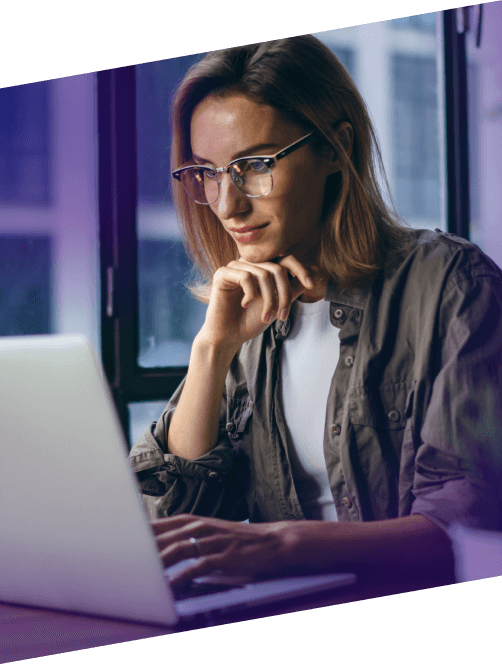